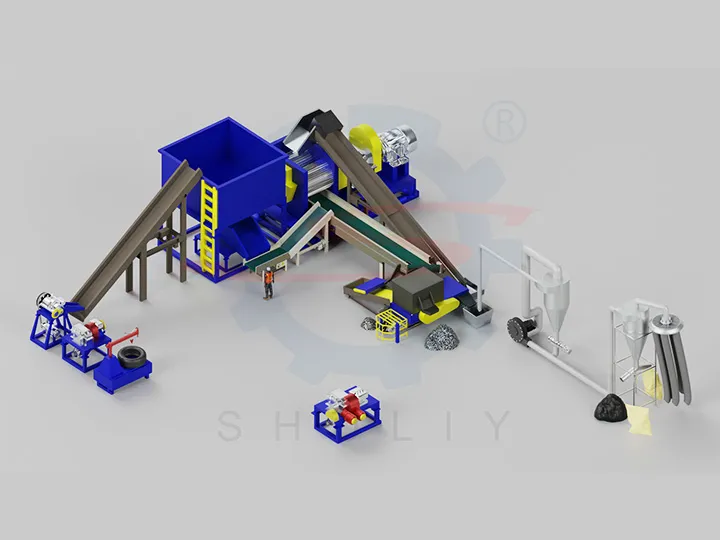
Semi-automatic Waste Tire Recycling Plant
The semi-automatic waste tire recycling plant is a practical and cost-effective solution for processing used tires into rubber powder or granules. Designed for tires with a diameter of less than 1200mm, this line combines manual and automated processes to achieve efficient tire recycling with high output quality.
Adjustable Output and Applications
The final rubber powder or granule size can be adjusted according to customer requirements. Thanks to the dual magnetic separation and fiber removal system, the rubber purity can reach over 99%.
The recycled rubber powder or granules can be widely used in:
- Artificial turf infill
- Rubber running tracks (including airfield and sports fields)
- Mouse pads
- Reclaimed rubber production
- New tire manufacturing
Equipment Included and Working Process
This waste tire recycling plant consists of the following main machines:
- Tyre sidewall cutter: Cut off the sidewall of the tyre containing the rim.
- Waste tire strip cutter: Cut the tyre with the rim removed into strips.
- Tyre block cutting machine: Cut the rubber strips into 3-5cm pieces.
- Tire steel wire separator: Effective separation of the rubber from the rim of the tyre section cut by the sidewall cutter.
- Rubber Crusher: The automated chain consists of crushing, screening, and magnetic separation units that efficiently process tire blocks into high-purity rubber powder with the right particle size and fewer impurities.
- Fiber separator: Separation of fine fibres in the rubber powder to achieve 99% purity.
This video provides a comprehensive overview of the entire working process of the semi-automatic tire recycling line. The first half of the process involves manual pre-treatment steps, including bead cutting, strip cutting, block cutting, and steel separation. These steps typically require 2 to 3 workers to manually operate and ensure that the tires are properly dismantled into sizes suitable for further crushing.
The latter half is handled by automated equipment, which performs crushing, screening, and magnetic separation, ultimately producing high-purity rubber powder or granules.
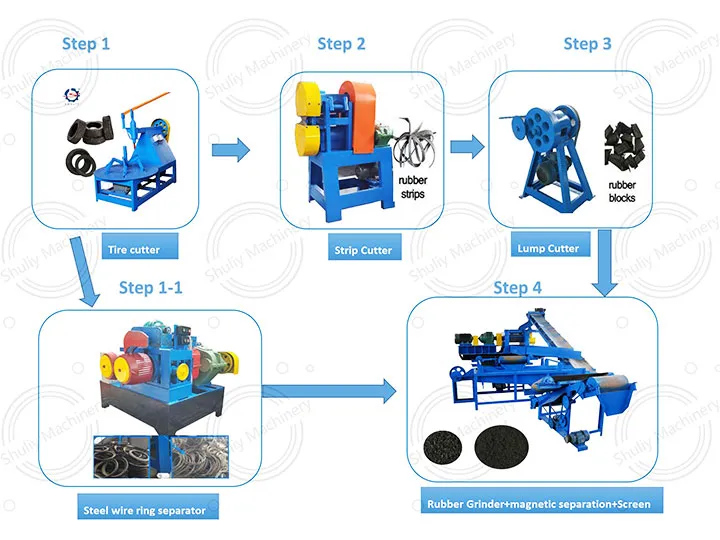
Features of the Semi-automatic Waste Tire Recycling Plant
- High Cost-Performance Ratio: The equipment requires relatively low investment, making it ideal for small to medium-sized recycling plants to start production.
- Adjustable Output Size: The size of rubber powder or granules can be flexibly adjusted according to customer requirements, suitable for various application scenarios.
- High Purity Output: Equipped with dual magnetic separators and a nylon fiber separator, the final rubber powder can reach over 99% purity with stable quality.
- Customizable Design: The system can be customized based on the customer’s plant layout, capacity needs, and product specifications.
FAQs of the Semi-automatic Waste Tire Recycling Plant
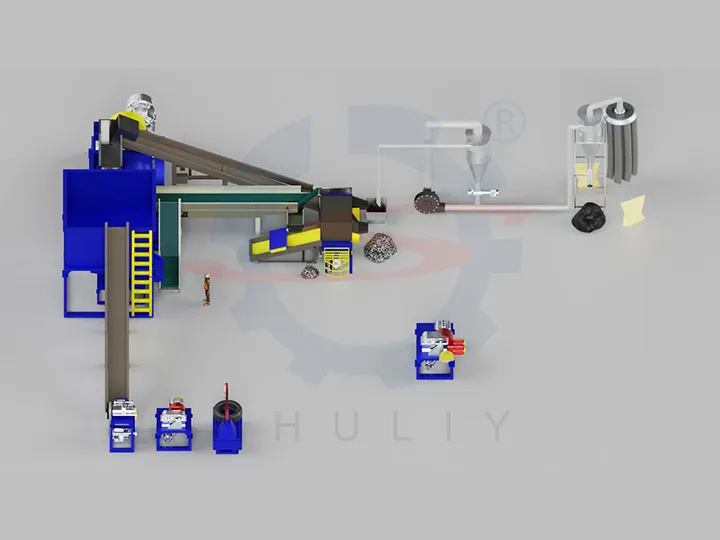